
Semiconductors
NOVEL APPROACH FOR RECLAIMING SEMICONDUCTOR WASTEWATER SAVES OPERATIONAL COSTS
Gradiant was uniquely qualified to deliver a resilient solution to treat and reuse wastewater for one of the largest global semiconductor manufacturers. The custom-designed system combined proprietary and conventional technologies to ensure robust treatment and reliable recovery. The client is also realizing higher recovery and additional capacity as the system is optimized.
Fast Facts
Location: Taiwan
End User: One of the World’s Largest Semiconductor Manufacturers
Solution: Industrial Wastewater & Recycling
Industry: Semiconductor
Feedwater Source: Combined Wastewater from semiconductor manufacturing
Technology: Bio-Infinity: BioCapture MBBR and Anaerobic Fluidized Bed (AFB) SCE: Fluidized Bed Crystallization (FBC)
System Capacity: 35,000 m3 /day
System Recovery: Up to 65%
Online Date: Commissioning (2021), Fully Online (2022)
Delivery Model: Design-Build (DB)
The Challenge
One of the world’s largest global semiconductor manufacturer contemplated numerous approaches to achieve water reuse targets issued by the local Science Park in Taiwan. Not only did the wastewater contain variable concentrations of total organic carbon, ammonia, and nitrates, but the space available for implementing a new treatment plant was minimal. This combination of design challenges, along with the intricacy of managing the project without disrupting ongoing operations proved to be too onerous for several providers, except for Gradiant.
The Solution
Gradiant and the client partnered to complete bench-scale testing of a multi-stage solution, demonstrating proof of concept and achieving treatment objectives. Knowing that the process would need to endure the variability of influent conditions (i.e., flow, concentrations), Gradiant conducted a pilot of the customized solution to validate its efficacy and resilience. This effort would also need to ensure that the plant could recover 55-65% of the influent flow of 35,000 m3 /day.
The elegant, compact solution for the complex wastewater incorporated several proprietary technologies, including:
- BioCapture for the removal of total organic carbon, ammonia, and urea, which can handle low biological loading yet unpredictable incoming wastewater flows
- FBC for the removal of hardness and phosphates, minimizing sludge production and overall solution footprint
- AFB for denitrification and total suspended solids removal, with a unique capability to handle low biological loading, yet highly variable, influent
The Benefits
With the optimized flowsheet for reuse, the client could recover roughly 20,000 m3 /day or 57% of this wastewater stream, potentially increasing further once the process is fully optimized.
By single-sourcing the solution with Gradiant, the client made quick, definitive design changes to enable more timely and efficient project delivery. The client anticipates being able to further increase capacity at the plant, where freshwater availability had previously been a constraint on production.
Due to the project’s overwhelming success, Gradiant has established itself as the partner of choice for future water reclamation projects. Gradiant will collaborate with the client at a new fab, where the goal will also be to recycle wastewater for beneficial reuse and to achieve critical sustainability goals.
Impact Stats
65%
Wastewater Recovery
50%
Waste Reduction using FBC over traditional technologies
10
years Experience in semiconductor wastewater treatment
20,000
m³ of Freshwater Generated Every Day
10-30%
Operational Cost Savings compared to Conventional Technologies
Figures & Images
Semiconductor Manufacturer’s LSR Process Flow Diagram
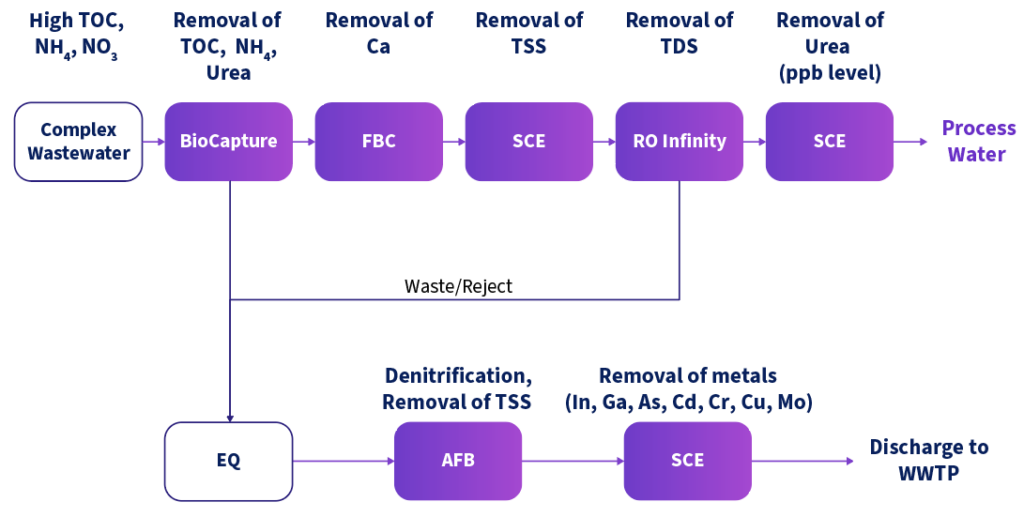
Legal Disclaimer
This document is for general information only. No warranty or guarantee whatsoever is given or implied and Gradiant is not bound by or liable for or by the information contained herein. Customer has the sole responsibility to determine whether the information in this document are appropriate for Customer’s use, including without limitation actual site, geographical, and plant conditions, specifications, requirements, disposal, applicable laws and regulations. This document is the intellectual property of Gradiant, including but not limited to any patent or trademark contained in this document. Distribution of this document is not and does not imply any transfer of Gradiant’s intellectual property.
Gradiant, the Gradiant Logo, and all service marks denoted with ™ or ® are owned by affiliates of Gradiant Corporation unless otherwise noted. © 2024 Gradiant.