CURE Chemicals in Industrial Manufacturing
A SYSTEM-WIDE APPROACH DELIVERS DELIGHT
A Gulf industrial manufacturer now finds time to focus on continuous improvement, instead of maintenance, by adopting Gradiant's recommendation for whole-system best practices combined with a bespoke CURE Chemicals blend that has delivered flawless performance without unplanned downtime for three years and counting.
Fast Facts
Location: Gulf Region
Application: Boiler Systems
Solution: Boiler System Treatment
Industry: Heavy Industrial
Feedwater Source: Softener System
CURE Chemical: Oxygen Scavenger, Scale Inhibitor, Condensate Treatment
The Challenge
The Solution
Gradiant started with a whole-system evaluation, including the performance of the softener system with operational best practices recommendations to improve efficiency and reliability. We developed a bespoke CURE Chemical solution that combined the utility of an oxygen scavenger, scale inhibitor, and condensate treatment. Once implemented, the boiler system could operate efficiently and effectively within normal operating variability and accommodate fluctuations in high hardness input from the softener system. We supported the treatment program with ongoing twice-weekly monitoring, including detailed service reports and operational recommendations for the local operations team to ensure continuous system reliability, uptime, and lower overall operating costs.
The Benefits
We deployed our solution in 2020 and continue monitoring and maintaining this customer’s site with zero unplanned downtime since startup. The treatment program has exceeded the customer’s expectations, requiring nominal inspection during planned shutdown events due to the pristine condition of the boiler, which exhibits no reportable scale or corrosion. Consequently, the plant has yet to initiate any cleaning or repairs, which has enabled the customer to focus on continuous improvement instead of troubleshooting.
Impact Stats
>3 YEARS
of operation without unplanned maintenance
ZERO
unplanned downtime hours
ZERO
incremental inspection downtime
UP TO 5%
improvement in fuel efficiency
Figures & Images
Clean boiler
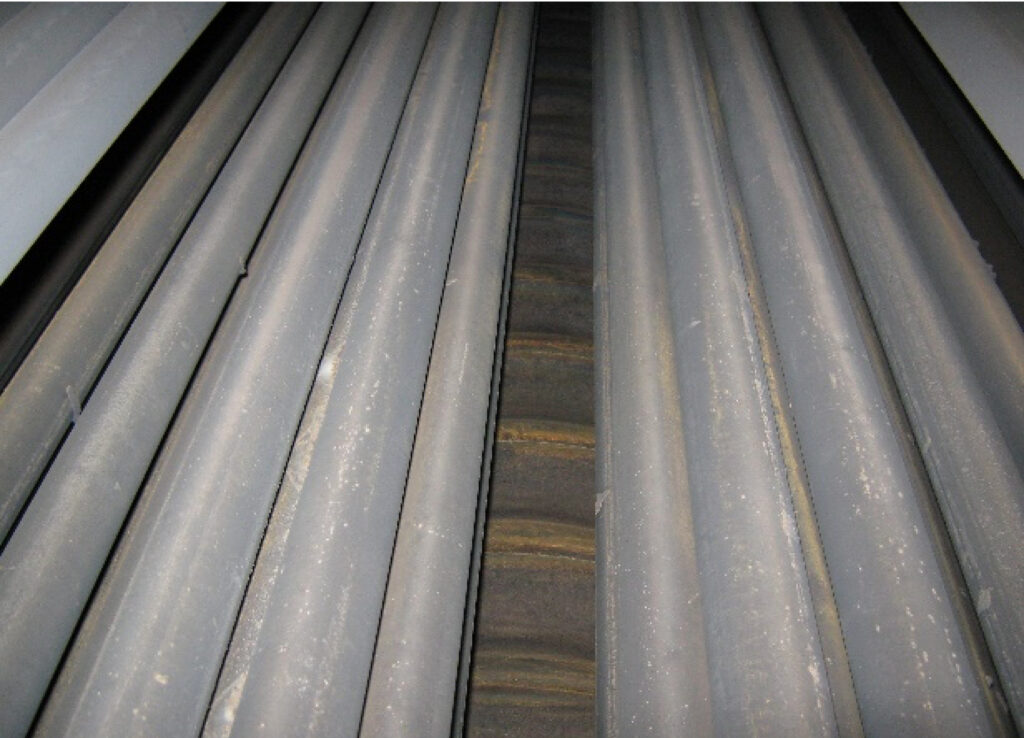
Twice-weekly sampling
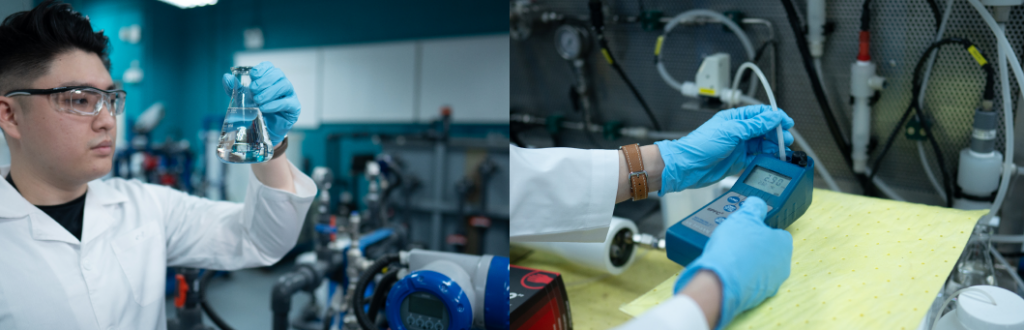